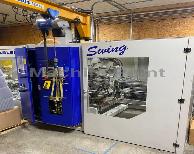
GABLER - SWING
Thermoformer. Machine has been used for testing new product so low usage Roll unwinder Rewinder Includes: W / 2009 ABUS 320-kg capacity jib crane, w/abused electric chain hoist w/ two-way pendant control, approximately 4' outrigger ...
2010 | 300046505 | GABLER