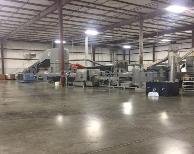
EREMA - INTAREMA 1714 TE
Single screw repelletizing line. Installation year 2018 Processed material PET 800-1000 kg/hr Material: Fibres. Origin of material: Industrial waste (recycler) Belt Conveyor FB_10000_1200_SH with Double Layer All Metal Detector INTAREMA® Process Combination 1714_TE Including shock...
2017 | 300045903 | EREMA