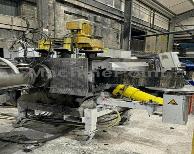
BRITAS - ABMF-0570-07
Screen changer for extruders. Automatic Band Melt-Filter Screen area capacity: 260 x 220 mm Accumulator: 7 Litre Electric power input: 57 KW Max. Pressure: 200 bar Operating temperature: max. 270°C Cooling water: Pressure: 3 — 4 bar Temperature: max. 15°C Cooling water qu...
2018 | 300046238 | BRITAS