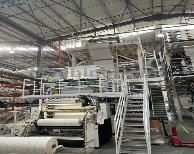
MACCHI - Coex 5
Coextrusion lines. 5 layers extrusion line Extruders 3x 45 mm, LD30 with hydraulic screen changers 2x 55 mm, LD30 with hydraulic screen changers Syncro gravimetric units, 4 components for each extruder 5 layers coextrusion die head with IBC mod TE551, insert range 2...
2021 | 300046553 | MACCHI